Advancing aero-thermal test capabilities
The demands of green vehicle development are placing a greater emphasis on the need for more advanced aero-thermal test capability, as John Komar, of the University of Ontario Institute of Technology, explains
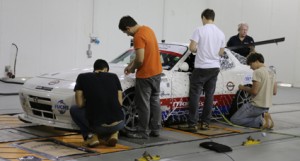
Automotive Centre
The global demand to improve fuel economy across a wide range of automotive vehicles continues to spawn developments in electric vehicle (EV) and hybrid electric vehicle (HEV) technology. Improved aerodynamics of the overall vehicle, specifically the reduction in drag force, contributes directly to the fuel economy of any vehicle type, especially at highway speeds. However, growing engine power demands, utilisation of sophisticated engine and underbody devices, and emission regulations have combined to make engine and underbody aerodynamic and thermodynamic (aero-thermal) management take an increasing role in the design process of new road vehicles.
As a specific challenge in green vehicles, the cooling of battery packs used in EVs and HEVs requires innovative solutions. There are therefore aggressive research programmes that focus on different cooling techniques, from phase-change material to liquid cooling, and natural and forced convective air cooling. Traditional aero-thermal studies on vehicles primarily focus on the engine, but this cannot be improved in isolation. Although air penetration into the vehicle engine bay improves cooling of the components, it also increases the overall aerodynamic drag of a vehicle.
Computational methods, such as computational fluid dynamics (CFD), have enjoyed rapid advancement in capability and speed and are therefore increasingly used in the design and development of aero-thermal management systems of EVs and HEVs. This has been an essential tool in the economics of fuel efficient vehicle development, in particular to help reduce the design cycle time to stay competitive. However, as the demands on fuel economy increase, so does the need to validate the predicted improvements in aero-thermal management. The answer is improved test techniques, specifically using wind tunnels.
Wind tunnel research
Aerodynamic wind tunnel (AWT) practitioners have addressed the critical area of ground simulation by employing moving ground systems and large test section flow area nozzles in order to improve the underbody flow field simulation accuracy. This in turn has provided better understanding of the interaction between external and underhood flows, such as optimisation of the external airflow with air dams and ducts to improve the cooling flow through the radiator.
Climatic wind tunnels (CWT) have traditionally been used to validate the thermal performance of vehicles in all weather conditions under full dynamic load, i.e. with the engine powering the wheels on a chassis dynamometer. The high installed capital and operating cost of CWTs has resulted in smaller test section nozzle flow area, no crosswind capability, and little or no ground simulation, which in turn has reduced underbody flow field simulation accuracy. Recent CWTs which have come online have larger flow area and some ground simulation attempts, such as boundary layer removal.
The CWT at the Automotive Centre of Excellence (ACE) at the University of Ontario Institute of Technology (UOIT) has gone one step further by including a chassis dynamometer in a large 11.5m diameter turntable which can yaw a vehicle relative to the oncoming wind to simulate crosswinds. Further, the test section nozzle can be increased from 7-13m2 by an increase in width as the car and chassis dynamometer combination is yawed to simulate crosswinds. This capability, which is unique in the world, is the first step in a planned continual upgrade of test capability to improve aero-thermal research and development. Already, underbody aerodynamic and thermodynamic test techniques have been developed which employ a fixed power heat source and flow field aero-thermal measuring equipment, such as an infrared camera, thermocouples and flow angle probes, to observe the influence of airflow temperature, wind speed and yaw angle on the convective heat transfer on the heat source. This experiment will serve to show practitioners the improvements in test technique already in place to enable better validation of computational tools.
ACE is the first testing and research facility of its kind in Canada. As a result, we are generating interest from people representing a broad range of sectors, including all automotive sectors and manufacturers, aerospace, transit, national defense, green energy, competitive athletes and the movie industry. They like the fact that they can perform their scientific research and engineering development using a $100M+ tool that is truly independent, highly secure and operated by a team of top notch engineers and technicians. It’s a place where Industry can work independently or collaborate with world class experts on Scientific Research and Engineering Development projects.
The next stage presently underway at the ACE CWT involves developing a capability to measure incremental aerodynamic response to changes in vehicle features such as air dams, spoilers, rear underbody diffusers etc. The focus is on integrating force and moment measuring capability into the chassis dynamometer-turntable system. The concept, which has already had a proof of concept demonstration test, involves four ‘pads’ with load cells upon which the vehicle tires make contact. This will enable incremental aerodynamic improvements to be made on the overall vehicle performance while monitoring the cooling flow pathways, followed almost immediately by thermodynamic performance changes associated with the overall vehicle aerodynamics using the same vehicle in the same facility with the same flow field simulation.
The next major step now in the investigation stage is to improve the test section nozzle flow quality and acoustics and incorporate a moving ground system which can be easily and quickly interchanged with the chassis dynamometer system. When this upgrade, which is currently in the initial grant application phase, is fully installed and functional, it will provide UOIT-ACE with a wind tunnel which can operate in modes that range all the way from a pure AWT to a conventional CWT, to an integrated aero-thermal facility. This will greatly enhance the focus already in place on collaborative research between academia and industry, with the aim to give researchers and clients around the world the opportunity to develop vehicle fuel efficiency which has been backed up with the most advanced test validation capability.
John Komar
Director, Automotive Centre of Excellence
University of Ontario Institute of Technology
[email protected]
ace.uoit.ca